ROCKETRY SA
OFFICIAL SOUTH AFRICA ROCKETRY ORGANIZATION
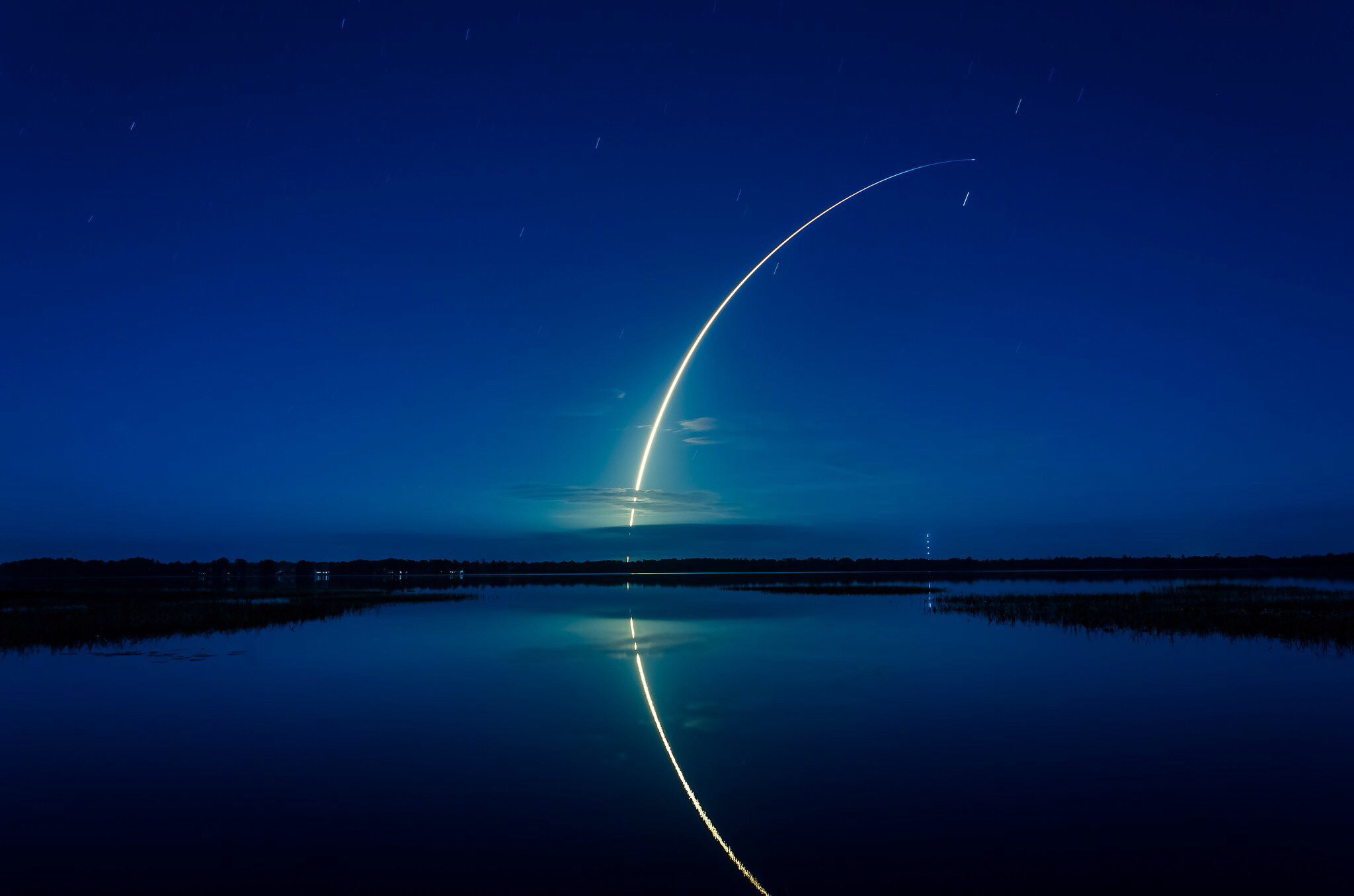
100% of all Donations go to the Children!
Sponsor & Donate Today to Support this Worthy cause..
ROCKETRY SA
We provide Policy & Procedures, Guidance and Administration for the Legal & Safe Participation in Rocketry activities within South Africa.
We Welcome Anyone with a Positive Attitude that has an interest in Science, Education, Engineering!
Join the Team
We encourage Member feedback and welcome You to make difference by joining the Team.
Volunteer
As a registered Non Profit Organization (NPO) we need You to get involved as a volunteer to help make Rocketry accessible in South Africa and to support Members.
Programs
Current Initiatives & Projects
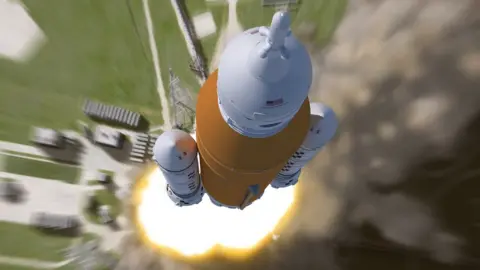
Model Rocketry
This is where the Journey starts.
With a little bit of theory to get you started, followed by “hands-on” learning to gain experience in building and launching small, rockets made from lightweight components.
Model Rocketry Fun, and is the foundation of Space Exploration!
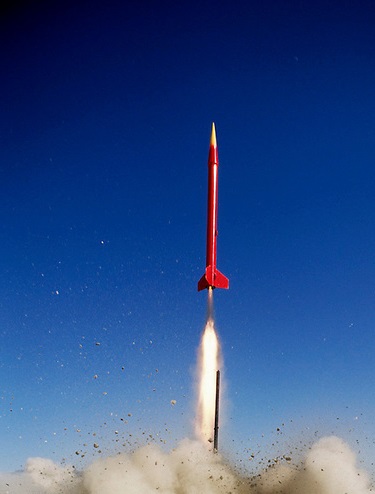
High Power Rocketry
Having mastered the basics you will likely want to build and launch bigger rockets, and this is the next step..
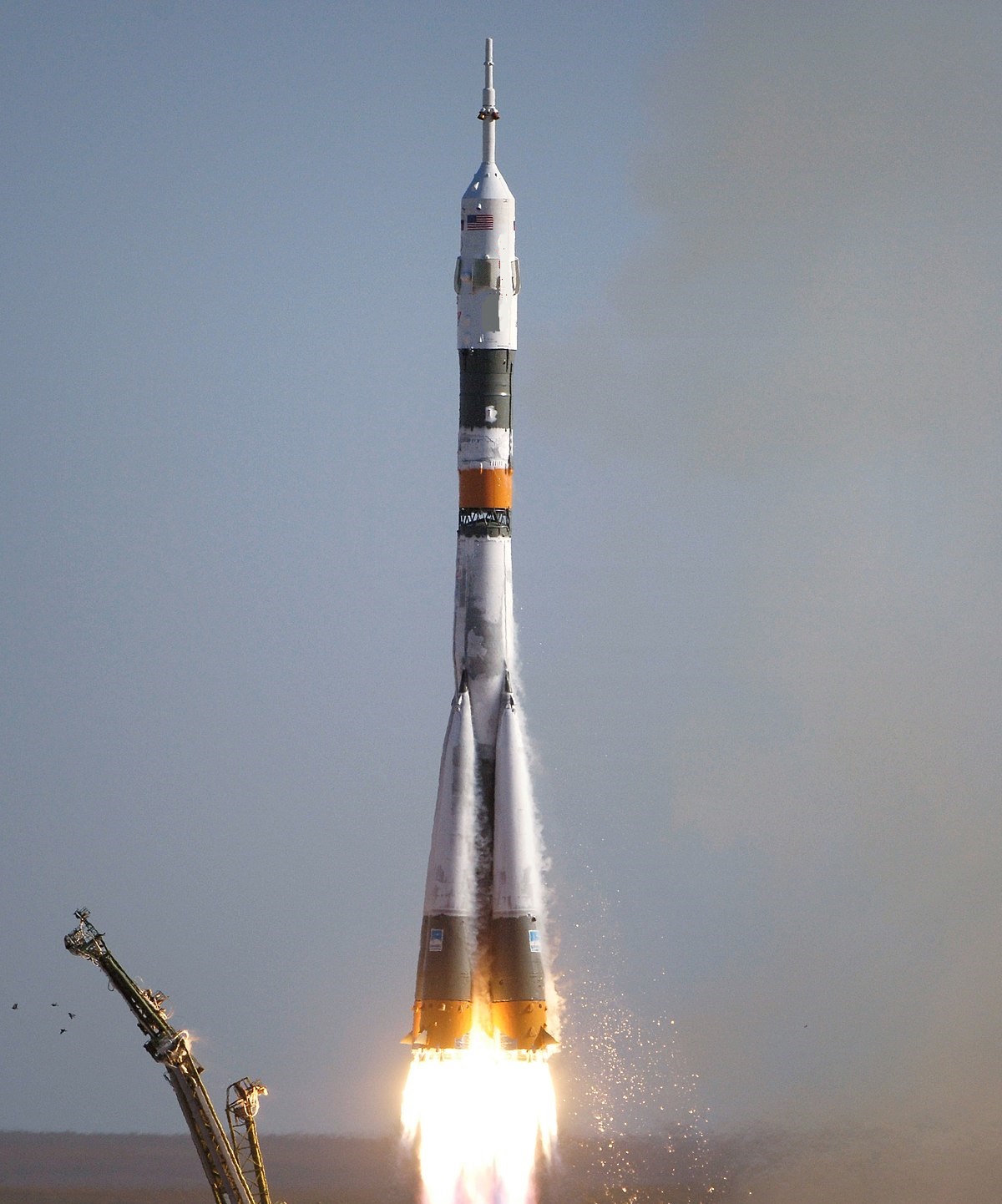
Amateur Rocketry
While tempting to dream of launching into space, there are advanced skills and science you need to master first.